Okay I very carefully prepped the mold as follows:
-smoke ONE cavity with butane lighter until it was very dark
-warmed up mold blocks (no handles) on hot plate
-took construction pencil and rubbed on ONE HP conical pin (casting surface only)
-using 100% cotton makeup remover pads, dribbled some MP lube on them and then carefully wiped the alignment pin holes and pins
-wiped guide screws of HP pins (cold)
-assembled mold blocks with HP pins and sprue plate
-put assembled mold on hot plate and got it hot
-filled mold with lead
-wiped sprue plate mold side and mold sprue plate side with lubed cotton pad
-put a couple drops of lube on pivot pin
-Then I let it got hot again until it stopped smoking.
I began my first casting session, 5 minutes long (roughly)
I produced 64 boolits, heres the stats:
-mold temperature approximately 500F preheated on hot plate
-lead temperature 750F (a few were done at 710F)
-lead is basically range scrap with maybe some tin added from a 111 solder bar
-ZERO wrinkles..seriously ZERO
-10 rejects, for the following reasons:
**4 with radiused base edge
**1 severely under-filled (not sure what happened)
**1 with dent on base (not from impact)
**4 with what seemed to be unusual porosity in sprue face
-Boolits dropped right from the mold. At most I needed to tap the HP guide pins with my gloved finger (and I mean tap)..dont even need to knock the handles with anything.
-I think the smoked cavity produces boolits with a kind of frosted/mottled appearance (acceptable)..
-It would seem smoking/graphiting is not needed here.
-Sprue is taken 5 seconds or more to solidify. I guess I should go down in lead temperature.
-I'm dropping them into a water bucket but its making big splashes....any good ideas to reduce this? On at least one cast water was in the mold when I went to pour.
-The main time consuming factor here is waiting for the sprue to solidify. How can I tell if I've hit the sweet spot? I dont want to produce wrinkles by lowering temps too much.
So at this rate I could produce 700+ an hour. But Im not going to push it that fast. 1000 in a couple days would be fine with me.
Pics show random 5 that are "good" and then the rejects
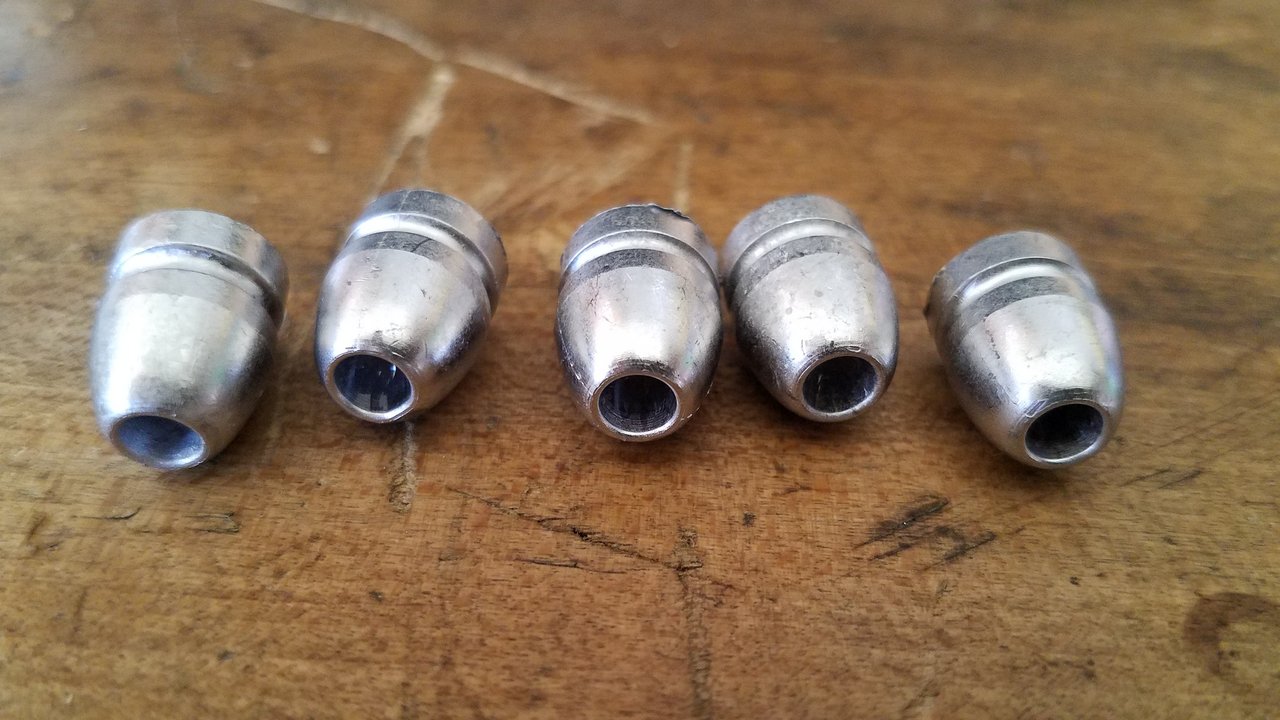